Maintenance Tips for Extending the Life of Your Pneumatic Cylinder
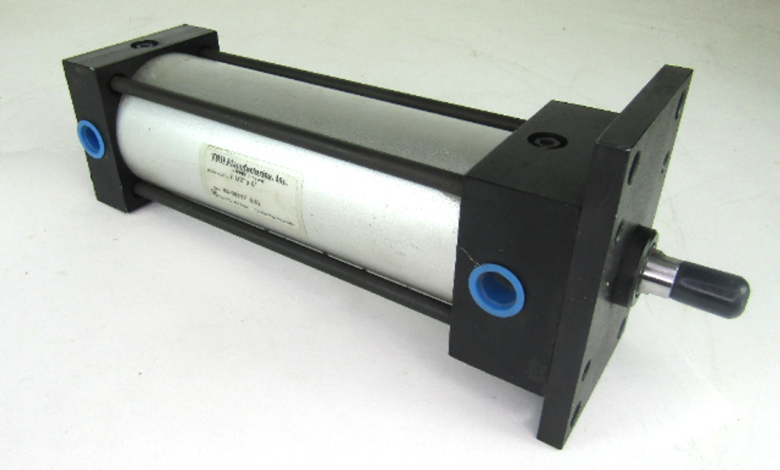
Air operated cylinders are used in a number of industries especially in automation and mechanical equipment. They are used to give the necessary mechanical force since a compressed air system only produces linear motion. However, similar to other critical parts of pneumatics systems, cylinders are bound to need a little maintenance at some point to keep them efficient, durable and effective. These measures make it possible for the companies to prevent episodes that force them to seek expensive repairs and to close down in the process. Here are some of the most helpful expert maintenance tips to follow that can help him/her to enhance the lifespan of his/her pneumatic cylinders.
Regularly Inspect for Leaks
Small amounts of leakage in a pneumatic cylinder will decrease its effectiveness and its ability to perform optimally. Some common sources of leaks are that the seals may be worn or some parts broken. Among other matters for which it is necessary to periodically look for signs of leakage are connection points and seals as well as the cylinder shafts. In case leaks are detected, you need to contact a professional engineer and fix problems as early as possible. To make accurate diagnoses and ensure quality seal replacement, it is recommendable to work with industrial automation inc.
Keep the Cylinder Clean
It is therefore always important to keep the working environment clean in order to have a longer pneumatic cylinder life. Dirt and other interferences that may form an abrasive mixture with the lubricant impinge on interior finishes such as seals, pistons, and shafts. It is also recommended that the exterior of the cylinder and its near environment should be cleaned frequently in order to minimize the accidental gathering of dirt that may enter the system. Also, check if air filters are clean or not, and if they work properly as they reduce dirt particles that may find their way into the pneumatic system.
Lubrication Is Key
To a larger extent, this element is critical in lowering the friction and wear of pneumatic cylinders. Lack of lubrication may also cause seals and other mechanical rubbing elements to fail earlier than expected. Ability of the cylinder lubrication system should be examined and the right amount of lubricant should be supplied. Infrequent lubrication should be done according to the manufacturer’s specifications and the kind of lubrication that should be used. Lubrication systems for pneumatic systems – Industrial automation INC has policies in place that may be helpful in aiding you choose the right lubrication systems for your pneumatic system to perform at its best.
Monitor System Pressure
It is recommended that the pressure levels in pneumatic system examples should be kept as close to the manufacturer recommendations as possible. Excessive or inappropriately low pressure in operation of a pneumatically controlled cylinder can cause system failure. High pressure may result in heating of the cylinder while low pressure leads to the production of an insufficient force output. Daily monitor the pressure of the system and make sure that it has the right pressure that is recommendable for the cylinder.
Perform Regular Seal Replacements
Seals refer to important commodities in pneumatic cylinders since their main function is to contain air and to ensure that no contamination gets into the cylinder. Seals, particularly dynamic seals, can become ineffective with time as they wear out owing to pressure and abrasive forces and vulnerability to environmental factors such as heat and corrosive substances. Check the seals and replace them often, if you should for the proper functioning of your machine. Application of pneumatic systems in the many operations such as in material handling or robotics comes with some common consequences; hence the need to put in place a preventive seal replacement program to avoid system breakdowns.
Keep Established Working Conditions
Parameters such as temperature and humidity can influence the functionality of pneumatic cylinders , depending on the operating conditions. The mechanical properties of seals are sensitive to temperature variation; when the temperatures rise, the seals may become soft and when the temperatures are too low, they may become rigid, and so they may end up leaking or losing pressure. Introducing high humidity to the system can bring in damp, which could react with metal casing. The efficiency of your pneumatic system will be optimum if the environmental conditions are observed as recommended.
Perform System Calibration
The pneumatic system of the robot is also checked periodically for calibration of the cylinders so that the system operates at the right specified rate. The last is the mechanical wear with time therefore the part may wear out, lose its precision which will lead to different problems in the whole system. It will help you check that the cylinders are performing as required and that the general production process is going right if the system is calibrated now and then.
Training Among Employees
It is as important to train the employees on what to look for that could be indicative of wear or a malfunction. To maintain that kind of environment in your team, most of the problems that would warrant expensive repairs will have already been detected for solution. These aspects make it important that employees were trained to run checks on the performance of the system in order to keep the cylinders running optimally.
Pneumatic cylinders create the backbone of numerous operating techniques; keeping those cylinders in ideal condition will ensure your operations’ efficiency and also help lengthen the cylinders’ life expectancy. These are, therefore, regular inspections, checking and replacing lubricants, sealing, and ensuring correct system pressures and alignments are checked and achieved, respectively, to avoid expensive downtime as well as increase the service life of your pneumatic systems. Other help is also available from experts in industries, for instance the industrial automation inc so as to get extra tips on how to keep the systems in good order at all times. The application of these best practices will not only minimize costs of maintenance but also enhance productivity hence augmenting the business profits that are an incomparable method of operation.
Also Read: https://usabizpro.co.uk/